The 7-Second Trick For Alcast Company
The 7-Second Trick For Alcast Company
Blog Article
The Buzz on Alcast Company
Table of ContentsAll About Alcast CompanyAlcast Company Can Be Fun For AnyoneAlcast Company Can Be Fun For EveryoneGet This Report about Alcast CompanyAlcast Company Fundamentals ExplainedThe Of Alcast Company
The refined difference exists in the chemical content. Chemical Comparison of Cast Light weight aluminum Alloys Silicon advertises castability by decreasing the alloy's melting temperature and boosting fluidity during casting. It plays a critical role in allowing elaborate mold and mildews to be filled precisely. Furthermore, silicon adds to the alloy's stamina and put on resistance, making it valuable in applications where durability is important, such as auto parts and engine parts.It also boosts the machinability of the alloy, making it less complicated to refine into ended up items. In this method, iron adds to the general workability of aluminum alloys. Copper boosts electric conductivity, making it useful in electric applications. It additionally improves deterioration resistance and contributes to the alloy's general toughness.
Manganese adds to the stamina of light weight aluminum alloys and boosts workability (aluminum foundry). It is generally used in functioned light weight aluminum items like sheets, extrusions, and profiles. The visibility of manganese aids in the alloy's formability and resistance to cracking throughout fabrication processes. Magnesium is a light-weight component that offers strength and impact resistance to aluminum alloys.
6 Simple Techniques For Alcast Company
It allows the production of lightweight elements with excellent mechanical properties. Zinc improves the castability of aluminum alloys and assists manage the solidification procedure throughout spreading. It enhances the alloy's strength and solidity. It is often discovered in applications where complex forms and great details are essential, such as attractive spreadings and certain automobile parts.
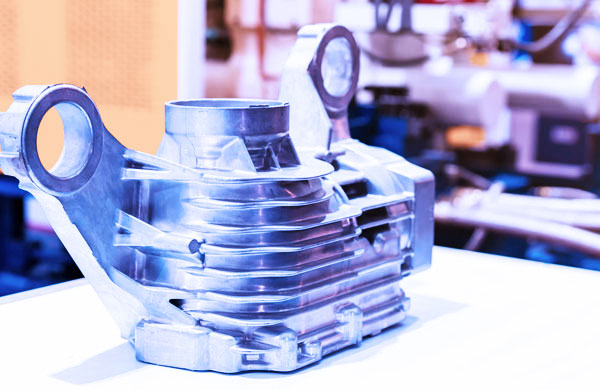
The key thermal conductivity, tensile strength, yield strength, and elongation vary. Among the above alloys, A356 has the highest thermal conductivity, and A380 and ADC12 have the lowest.
The Basic Principles Of Alcast Company
In accuracy spreading, 6063 is fit for applications where elaborate geometries and high-quality surface area coatings are paramount. Examples consist of telecommunication rooms, where the alloy's premium formability permits smooth and aesthetically pleasing layouts while maintaining structural stability. In the Illumination Solutions sector, precision-cast 6063 components create classy and efficient illumination components that call for detailed shapes and great thermal efficiency.
The A360 shows remarkable elongation, making it perfect for complex and thin-walled elements. In accuracy casting applications, A360 is well-suited for markets such as Consumer Electronic Devices, Telecommunication, and Power Tools.
The Alcast Company Diaries
Its distinct properties make A360 an important option for accuracy spreading in these industries, enhancing item durability and top quality. Foundry. Light weight aluminum alloy 380, or A380, is a commonly utilized casting alloy with several unique qualities.
In precision spreading, light weight aluminum 413 radiates in the Customer Electronics and Power Devices industries. This alloy's remarkable rust resistance makes it an exceptional selection for exterior applications, making sure lasting, long lasting products in the discussed markets.
The Buzz on Alcast Company
Once you have actually made a decision that the light weight aluminum die casting process appropriates for your project, a crucial following step is picking one of the most appropriate alloy. The light weight aluminum alloy you select will substantially impact both the casting process and the homes of the end product. Since of this, you must make your decision carefully and take an enlightened strategy.
Figuring out the most appropriate light weight aluminum alloy for your application will mean weighing a vast range of qualities. These relative alloy characteristics comply with the North American Die Casting Association's standards, and we've separated them right into 2 categories. The first category addresses alloy attributes that affect see the production process. The 2nd covers features affecting the homes of the end product.
The Single Strategy To Use For Alcast Company
The alloy you choose for die casting directly influences a number of elements of the casting procedure, like how easy the alloy is to deal with and if it is susceptible to casting problems. Warm cracking, additionally called solidification cracking, is a regular die spreading defect for aluminum alloys that can cause inner or surface-level rips or cracks.
Particular aluminum alloys are much more at risk to hot fracturing than others, and your option ought to consider this. Another typical defect discovered in the die casting of light weight aluminum is pass away soldering, which is when the cast stays with the die walls and makes ejection tough. It can harm both the cast and the die, so you must look for alloys with high anti-soldering buildings.
Corrosion resistance, which is already a noteworthy characteristic of aluminum, can vary substantially from alloy to alloy and is an important characteristic to consider depending upon the environmental conditions your item will be revealed to (Aluminum Castings). Wear resistance is an additional property commonly looked for in light weight aluminum items and can separate some alloys
Report this page